Fatigue and Fracture Research
Using Multiscale Material Models to Predict Mechanical Behavior
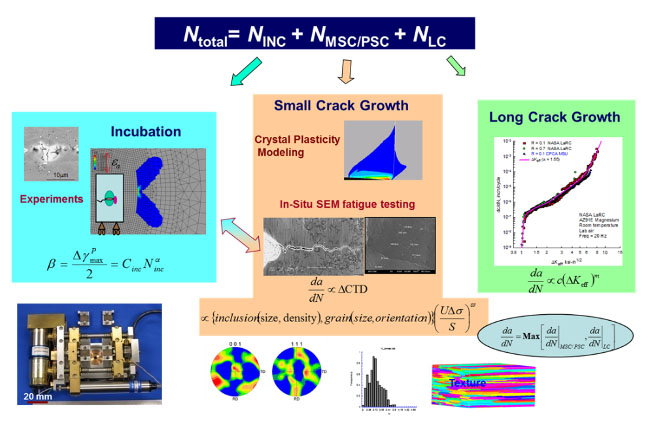
What’s Involved in this Research?
The developing of models (Mathematical equations) that are able to predict the life and resistance of a material is of great importance in engineering. Thus, this is an essential part of this research work: Providing mathematical models to predict the performance of machine components and structures.
The focus of this research is to experimentally characterize, to determine structure-property relationships, and to develop multiscale material models to predict mechanical behavior. This research involves a combination of experimental work and modeling as well as finite element simulations focusing primarily to build material models.
The goal is to develop micro-sensitive multiscale damage and fatigue material models to support a design simulation-based approach in order to optimize mechanical designs for vehicular structures.
Multistage Fatigue Model (MSF)
The life of structure or component depends on the magnitude and type of materials that are used and the kind of forces that are applied. The knowledge of the internal structure of materials gives insight into the mechanical properties such as the resistance of materials and structures to forces.
Fatigue of materials refers to the changes in properties of the materials resulting from the application of repeated loads. The origin of the word “fatigue” comes from the Latin meaning “tire.” In other words, fatigue represents the accumulation of damage in the material as a result of the application of repeated loads.
How You Benefit as a Student
Students are involved directly with hands-on projects; they can participate planning, designing, and conducting experiments, and helping to collect data as well. Not only are they collecting data, but they are also analyzing and interpreting data from real experiments. Undergraduate students can also investigate about new subjects and prepare reports of the investigation. They can provide new ideas to contribute to current projects also.
Students are operating state-of-the-art equipment to test and analyze materials. Simulating the performance of materials and structural components using finite element method (FEM) approaches offers them the chance to learn the most advanced FEM commercial packages.
Students get to perform stereological studies of materials, measuring, and determining the mechanical properties of materials. These studies require the use of state-of-the-art equipment to test and analyze materials such as SEM (scanning electron microscopy), electron backscatter diffraction (EBSD), universal monotonic and cyclic testing machines, and metallography facilities among others.
In these days, engineers in the mechanical design field are equipped with many computational tools to visualize, design, and simulate the performance of components and mechanical devices. With my research, students will have the chance to use computational tools and solve problems that engineers are facing on daily basis in the industry.
Research Professors
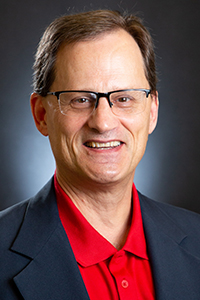
Mark Horstemeyer
B.S., M.S., Ph.D.
Distinguished Professor
Google Scholar Profile
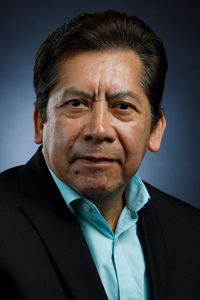
Dr. Marcos Lugo
B.S., M.S., Ph.D.
Associate Professor of Mechanical Engineering
Google Scholar Profile
How This Research Impacts Society?
Fatigue failure is the number one reason why structural materials break. Fatigue is not a new phenomenon, it has been known since many centuries ago. Ample research has been conducted in this field of study, however, this phenomenon is still not well understood. Mechanical fatigue failures have caused many injuries and financial loses. Despite of these failures, the number of failures compared to the number of successfully designed machine components and devices is small.
Nonetheless, the cost of such failures are enormous. Therefore, gaining a more precise understanding of the fatigue of this phenomenon will contribute to more profitable automotive and aerospace industries among others.
Articles
M. Lugo, W. Whittington, Y. Hammi, C. Bouvard, B. Li, D. Francis, and M.F. Horstemeyer, Chapter 11: “Using an Internal State Variable (ISV)–Multistage Fatigue (MSF) Sequential Analysis for the Design of a Cast AZ91 Magnesium Alloy Front-End Automotive Component”, in Integrated Computational Materials Engineering (ICME) for Metals: Concepts and Case Studies, Wiley 2018.
J. Hughes, M. Lugo, J.-L. Bouvard, T. McIntyre, and M.F. Horstemeyer, “Cyclic Behavior and Modeling of Small Fatigue Cracks of a Polycarbonate Polymer”, International Journal of Fatigue, 99, pp. 78-86, 2017.
Simsiriwong, J., Shrestha, R., Shamsaei, N., Lugo, M., and Moser, R.D., “Effects of Microstructural Inclusions on Fatigue of Polyether Ether Ketone (PEEK)”, Journal of Mechanical Behavior of Biomedical Materials, Vol. 51, pp. 388-397, 2015.
M. Lugo, J. E. Fountain, J. Hughes, J.-L. Bouvard, and M. F. Horstemeyer, “Microstructure-Based Fatigue Modeling of an Acrylonitrile Butadiene Styrene (ABS) Copolymer”, Journal of Applied Polymer Science, 131, 20, October 2014.
M. Lugo, J. B. Jordon, L. Hector, K. Solanki, J.D. Bernard, A.A. Luo, and M. F. Horstemeyer “Role of Different Materials Processing Methods on the Fatigue Behavior of AZ31 Magnesium Alloy”, International Journal of Fatigue, 52, pp. 131-143, 2013. https://www.sciencedirect.com/science/article/pii/S0142112313000662
M. Lugo, and S. R. Daniewicz, “The Influence of T-stress on Plasticity Induced Crack Closure under Plane Strain Conditions”, International Journal of Fatigue, 33, pp. 176-185, 2011.
M. Lugo, J. B. Jordon, M. F. Horstemeyer, M. A. Tschopp, J. Harris, and A. M. Gokhale, “Quantification of Damage Evolution in a 7075 Aluminum Alloy using an Acoustic Emission Technique”, Materials Science and Engineering A, 528, pp. 6708-6714, 2011.